What Is an NPT Fitting? Essential Guide for Effective Pipe Connections
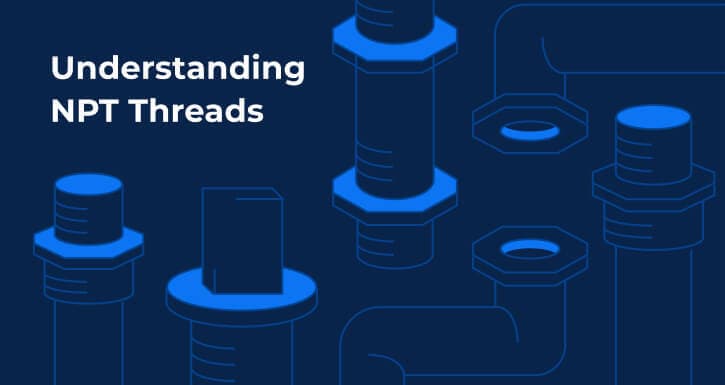
Have you ever tightened a pipe joint, only to find it still leaks no matter what you do? Preventing leaks is a common challenge in plumbing, engineering and construction projects. National pipe tapered (NPT) threads — also known as npt fittings — are designed to solve this problem by creating secure, tight seals.
But what is an NPT thread exactly? In this post, we’ll explore NPT threads, how they prevent leaks and how to select and install them properly.
What Is NPT Thread?
NPT threads are a standardized type of screw thread used on pipes and fittings. Unlike straight threads, NPT threads are tapered, meaning their diameter gradually becomes smaller from one end of the screw to the other. This gradual narrowing allows the threads to form a tight seal when pipes are connected. NPT threads are essential components in various industries, ensuring that pipe joints are secure and free from leaks.
The development of standardized pipe threads dates back to the 19th century. In the 1860s, American engineer William Sellers introduced a system of standardized screw threads, laying the foundation for modern thread standards in the United States. Around the same time, British engineer Sir Joseph Whitworth developed his own standard for screw threads in the UK.
As industries expanded, the necessity for consistent and compatible pipe fittings became clear. In the early 20th century, the American National Standards Institute (ANSI) adopted NPT threads as the U.S. standard for pipe fittings. This adoption ensured compatibility across manufacturers and improved safety in piping systems.
How Do NPT Threads Create Tight Seals?
NPT threads effectively prevent leaks thanks to their unique tapered design and the way they function during assembly. When properly installed, the threads compress to form a tight mechanical seal that stops fluids or gasses from escaping. Let’s examine the design features and sealing mechanisms that make NPT threads so dependable.
Design
NPT threads feature a tapered profile where the diameter decreases from one end to the other. This taper is standardized at 1° 47′ 24″ (1.7899°), corresponding to a 1/16-inch reduction in diameter for every inch of thread length. The threads themselves form a 60-degree angle at their apex, contributing to their ability to form a tight seal.
Sealing Mechanism
The tapered design allows the threads to wedge tightly together as they are tightened, creating a mechanical seal. As the male and female threads are screwed together, the tapering diameter forces the threads to compress, filling any gaps and preventing the passage of fluids or gasses.
Do NPT fittings need sealant? While NPT threads are designed to create a mechanical seal as they are tightened, using a sealant is highly recommended. Sealants, such as Teflon tape or pipe dope, help fill any tiny gaps between the threads, enhancing the leak-proof seal. In most cases, applying a sealant is essential for ensuring a secure connection, especially in high-pressure or high-temperature environments.
Leak-Tight Connections
This design ensures that even under pressure, the connection remains secure and leak-tight. The tighter the connection, the better the seal, which is why proper installation is crucial for NPT fittings.
Advantages and Challenges of NPT Fittings
NPT fittings deliver reliable and secure pipe connections but also have certain drawbacks. Understanding these advantages and challenges helps you select the right fittings for your specific needs.
Advantages | Challenges |
|
|
Comparing NPT with Other Thread Types
While NPT threads are essential for many pipe connections, other thread types are also commonly used in various applications. Understanding the differences between these thread standards ensures you select the most appropriate fittings for your specific projects.
NPT vs. British Standard Pipe (BSP)
BSP threads are commonly used outside North America. While they may look similar to NPT threads, they have different thread angles (55 degrees for BSP vs. 60 degrees for NPT) and pitch. NPT and BSP threads are not interchangeable, and attempting to pair them will likely result in leaks or thread damage.
NPT vs. National Pipe Straight (NPS)
NPS threads are straight (parallel) threads, unlike the tapered NPT threads. NPS threads do not provide a seal on their own and typically require a sealant or O-ring. They are used in applications where a mechanical connection is needed without the sealing function provided by NPT threads.
NPT vs. National Pipe Taper Fuel (NPTF)
NPTF, also known as Dryseal threads, are similar to NPT but designed to create a seal without the need for sealants. The threads are engineered with flat tops and bottoms, allowing direct contact between the metal surfaces to form a tight seal.
To highlight their key differences and uses, the following table compares NPT, BSP, NPS and NPTF thread types.
NPT | BSP | NPS | NPTF | |
Thread Type | Tapered | Tapered | Straight | Tapered |
Thread Angle | 60 degrees | 55 degrees | 60 degrees | 60 degrees |
Sealing Mechanism | Tapered seal using thread compression | Tapered seal using thread compression | Seal using sealant or O-ring | Metal-to-metal contact (Dryseal) |
Interchangeable? | No | No | No | Sometimes |
Common Applications |
|
|
|
|
Common Uses of NPT Fittings in Different Industries
NPT fittings are used in multiple industries to ensure secure and leak-resistant pipe connections. Their adaptability makes them suitable for a wide range of applications, from everyday plumbing to specialized industrial systems. Below are some primary uses of NPT fittings in various sectors:
- Plumbing. In both residential and commercial plumbing, NPT threads are commonly used for connecting pipes and fixtures, ensuring a watertight seal that prevents leaks.
- Engineering. Engineers use NPT fittings in systems that require robust and reliable pipe connections, such as hydraulic and pneumatic systems.
- Construction. Construction projects often involve extensive piping for water, gas and other utilities. NPT threads provide a standardized method for connecting these systems safely.
- Oil and gas. In the oil and gas industry, NPT fittings are used for connecting pipelines and equipment, ensuring secure and leak-proof transmission of hydrocarbons and other fluids.
- Pharmaceutical manufacturing. In this sector, NPT threads are employed in sterile piping systems and equipment connections, in order to maintain clean environments and prevent contamination.
Selecting the Right NPT Fittings for Specific Applications
Choosing the appropriate NPT fittings involves evaluating the material, size compatibility and pressure ratings to match the specific needs of your application. Understanding these factors ensures secure and efficient pipe connections tailored to your project’s requirements.
Material Considerations
- Brass: Ideal for water, oil and gas applications due to corrosion resistance
- Steel: Suitable for high-pressure applications but may require protective coatings to prevent rust
- PVC: Best for low-pressure and non-metallic applications, offering resistance to corrosion and chemicals
Size and Compatibility
Selecting the correct size ensures a proper fit and seal. Refer to standardized NPT thread sizes and dimensions when choosing fittings.
NPT Thread Sizes and Dimensions | ||
NPT Size (inches) | Outside Diameter (inches) | Threads per Inch |
1/8 | 0.405 | 27 |
1/4 | 0.540 | 18 |
3/8 | 0.675 | 18 |
1/2 | 0.840 | 14 |
3/4 | 1.050 | 14 |
1 | 1.315 | 11.5 |
Note: These dimensions are based on ANSI B1.20.1 standards. Always refer to manufacturer specifications for precise measurements and to ensure compatibility with your specific applications.
Pressure Ratings
Always consider the pressure ratings of the fittings to ensure they meet the requirements of your application. Using fittings below the necessary pressure rating can lead to failures and safety hazards.
Best Practices for Installing and Using NPT Fittings
Installing NPT fittings correctly is crucial for maintaining leak-proof connections. The best practices outlined below provide clear guidance to ensure your pipe installations are secure and efficient.
Preparation
- Inspect threads: Ensure that both male and female threads are clean and undamaged.
- Apply sealant: Use appropriate thread sealant or Teflon tape to enhance sealing capability.
Installation Process
- Wrap threads: If using Teflon tape, wrap it around the male threads in a clockwise direction.
- Start connection: Hand-tighten the male fitting into the female fitting.
- Tighten: Use a wrench to tighten the fitting according to recommended torque values.
Torque Values and Number of Turns |
||
NPT Size (inches) | Turns Past Finger Tight | Torque (ft-lbs) |
1/8 | 2–3 | 10–15 |
1/4 | 2–3 | 15–20 |
3/8 | 2–3 | 20–30 |
1/2 | 2–3 | 30–40 |
Sealants
Using thread sealants or Teflon tape helps fill gaps between threads, enhancing the seal and preventing leaks. Do NPT fittings need sealant? While NPT threads are designed to create a seal, applying a sealant is recommended for optimal leak prevention.
Common Mistakes to Avoid
- Over-tightening: Can damage threads and compromise the seal
- Using insufficient sealant: May lead to leaks; always apply sealant as recommended
- Cross-threading: Misaligning threads can damage fittings; always start threading by hand
NPT Threads for Optimal Pipe Connections
Secure and leak-free pipe connections rely on technicians selecting the right NPT fittings and following proper installation practices. By understanding the design features, material options and best practices discussed in this guide, you can ensure the reliability and efficiency of your piping systems.
To further support your projects, download our BSP & NPT Threads: Your Essential Conversion Guide, which offers detailed comparisons of thread standards, accurate conversion charts, practical selection tips and precise measurement methods. Whether you’re navigating complex industrial systems or handling everyday plumbing tasks, this guide will empower you to make informed decisions every time.