Ball Valve Sizes: How To Choose The Right Ball Valve Size
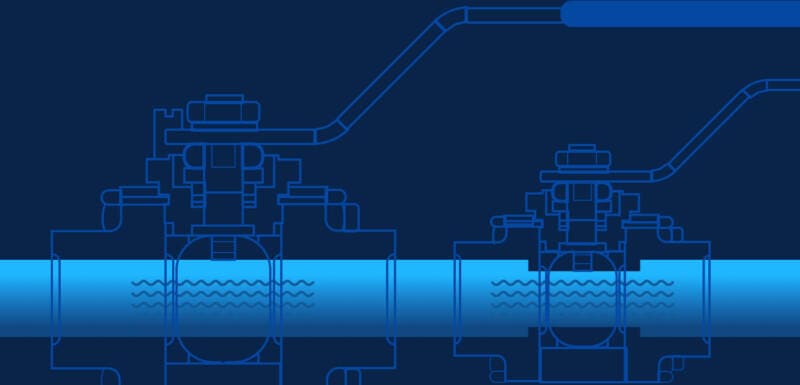
In the engineering and manufacturing sectors, there’s a particular phrase that rings true: “The devil is in the details.” This is especially evident when it comes to ball valve sizing — a facet that carries significant influence in piping system operations.
The right size ball valve can bolster system performance, longevity and even economic viability. On the other hand, an ill-suited size may invite inefficiencies, premature wear and tear or, worst-case scenario, system failure. Here, we navigate the complexities of ball valve sizing, shed light on key considerations and provide guidance to help you make informed decisions that optimize system performance.
Understanding Ball Valve Sizing
At its most fundamental level, ball valve sizing is about aligning the valve dimensions with the requirements of a specific piping system. The goal is to ensure that the chosen valve operates harmoniously with the system’s pressure, flow rate and temperature requirements, resulting in seamless operation and peak productivity.
Different types of ball valve sizing standards exist, but two of the most prevalent are nominal pipe size (NPS) and diameter nominal (DN). While NPS refers to the nominal diameter of the pipe, DN is its metric equivalent. It’s pivotal to grasp the nuances of these measurements and their implications on system operations. After all, improper valve sizing can lead to inefficiencies and even cause potential damage to the system.
Factors to Consider When Choosing Ball Valve Sizes
Identifying the right ball valve size for your needs is a calculated process that requires careful consideration of several elements, including:
- Flow rate: It’s crucial to understand that the flow rate, which refers to the speed at which fluid travels through a system, should be calculated based on the valve’s port size rather than the pipe size of the valve. This is a common misconception and an essential distinction for accurate flow rate measurement. Flow rate is commonly expressed in gallons per minute (GPM) or liters per minute (LPM).
- Pressure drop: This term signifies the decrease in fluid pressure resulting from frictional losses as fluid flows through the system.
- Pipe diameter: The width of the pipe plays a significant role in valve selection as it influences the flow rate and system pressure.
- Application requirements: Depending on the unique needs of the application, different valve sizes, materials or configurations may be necessary.
Choosing the Right Ball Valve Size in 4 Steps
Selecting the right ball valve size may seem complex, but breaking it down into a series of manageable steps can simplify the journey toward optimal performance:
Step 1. Determine the flow rate: The flow rate refers to the volume of fluid passing through your system within a specified time frame. Usually, it is measured in gallons per minute (GPM) or liters per minute (LPM). This can be calculated using the formula Q=VA, where Q is the flow rate, V is the velocity of the fluid, and A is the cross-sectional area of the pipe.
However, this typically involves complex considerations of fluid dynamics, and in many cases, this information will be provided in the specifications of your system or can be measured using flow meters. If you’re unsure about how to calculate flow rate, feel free to use our handy flow rate calculator for a quick and accurate estimation.
Step 2. Calculate the pressure drop: After determining the flow rate, you need to calculate the pressure drop, which is the reduction in fluid pressure as it flows through the system. This is commonly caused by friction loss, changes in height or the narrowing of the pipes. It can be calculated using various formulas depending on the fluid, pipe size and pipe length. Again, these are typically complex equations, and in most cases, pressure drop will be listed in your system specifications or can be measured using pressure sensors.
Step 3. Determine the pipe diameter: The pipe diameter is another critical factor. You need to know your system’s pipe diameter to match the size of the valve. The diameter will directly influence the flow rate and the system pressure, and it should correspond to the valve’s NPS or DN.
Step 4. Choose the valve size based on calculations: After gathering all the necessary information and conducting the appropriate calculations, you can then determine the appropriate valve size. This selection should be done meticulously, factoring in the flow rate, pressure drop and pipe diameter to ensure that the valve complements the system’s requirements.
Remember that this process is a guideline, and it’s essential to account for the specific demands and conditions of your system. Consider the materials that will be passing through the valve and the environment it will be operating in, and always consult with a professional or your system’s manufacturer if you’re unsure.
Common Ball Valve Sizes and Their Applications
Navigating the spectrum of ball valve sizes involves recognizing the unique capabilities and constraints each size brings to your specific application. This decision not only shapes system efficiency but also dictates the functional capacity of your setup. Here’s a breakdown of commonly used ball valve sizes, their ideal use cases and the inherent advantages or limitations they carry.
Small ball valves (below 1/2 inch):
- Typical applications: They are perfect for precision applications where flow rate is not critical, such as fluid filling systems or instrumentation.
- Pros: They offer higher precision and are ideal for systems necessitating control at lower flow rates.
- Cons: They may not be suitable for situations requiring high-volume flow due to their small size. A v-port ball may be required for applications requiring extremely precise flow control.
Medium ball valves (1/2 inch to 2 inches):
- Typical applications: Versatile and adaptable, they are found in diverse settings, including residential water systems, HVAC units and automotive systems.
- Pros: They strike a balance between flow rate and control, making them suitable for a wide range of applications.
- Cons: They may not be ideal for industrial applications involving high-pressure or high-flow rates.
Large ball valves (above 2 inches):
- Typical applications: Industries like oil and gas primarily use these valves for pipelines, power plants and industrial manufacturing, where large flow rates are typical.
- Pros: They are capable of handling high flow rates and are typically designed to withstand tough conditions.
- Cons: Their size and weight may make them unsuitable for more delicate or precision applications.
Always remember that the valve is merely one factor influencing the overall flow rate of the piping system. Generally, a valve port smaller than the piping won’t restrict most systems. The specifics of your system will ultimately determine the most suitable ball valve size.
Ball Valve Sizing Final Thoughts
Choosing the perfect ball valve size is meticulous and demands a thorough understanding of your system’s requirements. It’s a complex endeavor that involves several calculations and evaluations, but the payoff is significantly improved system performance and efficiency.
However, remember that choosing the right ball valve size is just one piece of the puzzle. Several other factors can determine the right ball valve for your operation, including product specifications, actuation options, materials, supplier considerations and more.
To simplify the process and ensure you have all the necessary information, we’ve created a comprehensive guide, 15 Factors to Consider Before Your Next Industrial Ball Valve Order. This resource not only provides more details about ball valve sizes but also offers valuable insights about different suppliers, essential testing and QA processes and vital certifications.
15 Factors to Consider Before Your Next Industrial Ball Valve Order
This guide includes everything you need to know before placing your next industrial ball valve order.