Flanged vs. Threaded Valve Connections
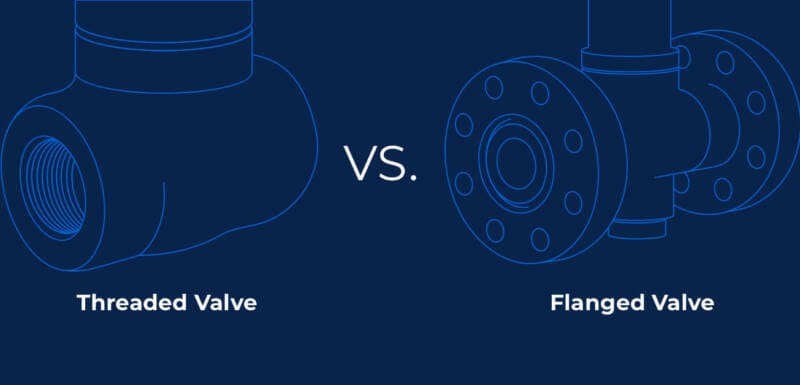
With many different types of valve connections available, it’s important to choose the right one in order to connect your valves and pipes together to prevent leaks. When selecting the best valve connection type for your process components and piping systems, there are several different categories of valve connection types to consider.
Two of the most widely used valve connections are flanged and threaded, and each type serves a specific purpose depending on the application in which it is being used.
Read on to learn more about flanged vs threaded valve connections and which offers the best alternative for your specific application.
What Are Flanged Connections?
In piping systems, a flange is a projecting rim or collar on a pipe or pressure vessel used to create a sealable joint with another flange pipe or pressure vessel. Many types of flanged connections require welding or gasket bolting to hold the pipe fittings together. However, some other types of this ring-shaped device offer alternatives to welding and can be easily disassembled for shipping, routine inspection, maintenance and replacement.
Flanged valve connections are commonly used in applications with:
- Large pipe sizes
- High-pressure
- Jobs that call for high joint integrity
Some of the most common types of flanged valve connections include:
- Blind flange: used to close the end of a pipe or to close a pipeline to prevent leakage or flow
- Lap joint flange: used by slipping over a pipe, which enables it to swivel around the pipe and facilitate the lining up of opposing flange bolt holes
- Slip on flange: used frequently in the pipes, valves and fittings (PVF) industry and connects via two filet welds
- Socket weld flange: used by attaching a socket weld joint to the pipe
- Threaded flange: used frequently in smaller piping systems and includes a threaded connection inside the flange bore, which does not require welding
- Weld neck flange: used to prevent turbulence and increase flow by precisely matching the inside diameter of the pipe
Flanges can be made from standard materials such as stainless steel and carbon steel or from more specialized materials designed for specific jobs. Flanged connection subtypes include:
- Flat face
- Raised face
- Ring joint face
- Tongue and groove
- Male & female
Flanged valve connections can deliver many benefits when used appropriately. For example, flanged connections:
- Allow piping spools to be assembled without welding
- Can be manufactured in many different piping spool formats
- Do not require painting/blasting
Although flanged connections can be advantageous when used under the right circumstances, they may also present some limitations. For example, flanged valve connections:
- Are expensive when used to insulate flanged pipes
- Require more space
- Are more prone to leaks
What are Threaded Connections?
Unlike flanged connections, which utilize multiple parts to fit piping components together, threaded connections are fitted with matching grooves (one set of grooves on the outside and the other on the inside).
Threaded connections are considered one of the oldest forms of joint connections, and they are still very popular today, as they allow for a more compact and efficient connection between pipe and valve.
Most threaded valve connections include a female threaded end connection that easily connects to a male threaded pipe. However, some of these devices are fitted with male threaded connections as well. Some even include both male and female threaded connections on either end.
Threaded valve connections are commonly used in a wide variety of applications and are particularly popular in applications with smaller pipe sizes (3” and under).:
Some of the most common types of threaded valve connections include:
- NPT: National pipe thread tapered, the US standard for tapered threads used in pipes and fittings, which pulls tight to make a fluid-tight seal.
- NPS: National pipe straight, a standard for straight (non-tapered) threads used in pipes and fittings that, similar to BSPP, requires a gasket or sealant to ensure a fluid-tight connection.
- BSPT: British standard pipe taper threads that include tapered threaded connections and a 55-degree angle of the thread flanks, which does not allow for a fluid-tight seal.
- BSPP: British standard pipeline threads, which do not create a fluid-tight seal on its own but rather pull together two threaded mating parts.
Threaded valve connections are typically available in two subtypes:
- Male vs. female
- Straight vs. tapered
There are several advantages to using this type of valve connection. Threaded valve connections:
- Are quick to install
- Are suitable for low-medium pressure applications and certain high-pressure applications
- Generally require less space than flanged connections
- Are relatively inexpensive
While they can be the right choice in certain applications, threaded valve connections may have some drawbacks. A few notable disadvantages are that threaded valves:
- Are not usable in very high temperature or very high-pressure applications
- Are not as easy to disassemble and service as flanged connections
- May be less foolproof to install as they can be over or under-tightened during installation or maintenance
What is the Price Difference Between Flanged and Threaded Connections?
When it comes to cost, threaded valve connections generally cost substantially less than flanged valve connections. The difference in cost between the two connection types is due to the multiple parts and various structures of flanges. However, despite the cost-savings associated with threaded valve connections, they offer less operational flexibility and are primarily only useful in low-pressure piping systems.
Ready to get started on your next utility project? Check out our guide to Valve Actuators to make sure you’re on the right track.
Your Complete Guide To Valve Actuators
A comprehensive introduction to valve actuators, covering power sources, failsafes, questions to ask and more.