Pneumatically vs. Electrically Actuated Ball Valves: Which Should You Use?
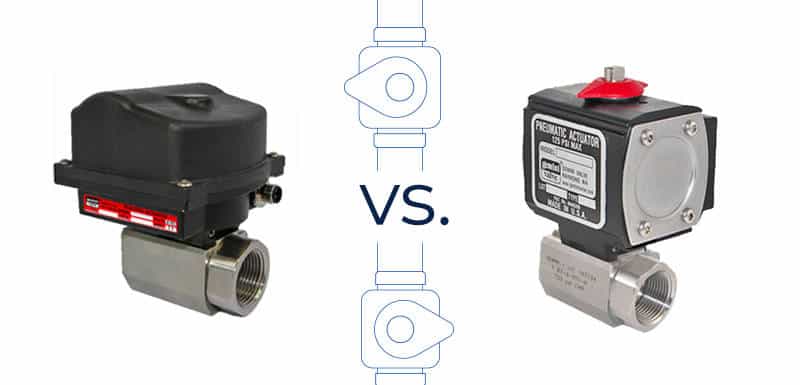
Pneumatic vs. electric actuators — which is best for your application? In general, pneumatically actuated ball valves serve the same purpose as electrically actuated ball valves: to control the flow of media.
Both types of actuation have their pros and cons, so it’s important to be sure you select the right one for your intended application. We explain the basics below.
First, a Note About Ball Valves
If you’re not familiar with how a ball valve works, it’s pretty simple. A ball valve is a quarter turn valve that uses a ball with a hole drilled through it to control the flow of media. The hole is referred to as the port or orifice and when opened, it’s aligned with the valve body to permit flow. The ball is contained within a body and uses a stem that is connected to the output shaft — in this case, of a pneumatic or electric actuator. From the closed position, it’s turned 90° counterclockwise to open and 90° clockwise to close.
What is a Pneumatic Actuator?
Pneumatic actuators rely on compressed air or gas as the primary power source. These actuators don’t require a motor, but electricity is necessary when paired with an integral solenoid valve which is commonly referred to as a pilot valve.
Remote piloting can also be achieved utilizing the air supply port(s). The solenoid (pilot) valve receives an electric signal which energizes its coil and allows air to flow either in or out of the pneumatic actuator, subsequently opening/closing the ball valve.
Two types of pneumatic actuators are available: double-acting and spring-return. Both utilize a rack and pinion design, which is well known for its reliability and durability.
- Double-Acting Pneumatic Actuated Ball Valves
Double-acting uses air to move internal pistons (racks) in two directions, which rotates the actuator pinion 90°. The pinion is connected to the ball valve stem and opens or closes the ball valve as it rotates. Double-acting actuators will return to the normal position when power is lost and can be configured as either normally open or normally closed. In the event that air supply is lost, double-acting actuators will stay in their current position. - Spring-Return Pneumatic Actuated Ball Valves
Spring-return uses air to move the internal pistons in one direction and springs in the other. These actuators are normally supplied as an air to open, spring to close operation, but can be supplied as air to close, spring to open. The mechanical springs can be susceptible to spring fatigue, making double-acting a better choice for high-cycle applications. Spring-return actuators will fail to the normal position in the event of either power failure or loss of air supply. - Double-Acting with Failsafe
Gemini Valve now offers an industry first double-acting pneumatic actuator with failsafe. This combines the durability of a double-acting actuator with the failsafe normally only offered by spring-return models. The actuator operates in a double-acting configuration until power or air pressure is lost, and springs engage automatically to return the valve to the normal position.
Pros & Cons of Pneumatic Actuators | |
Pros | Cons |
|
|
What is an Electric Actuator?
Electric actuators (sometimes known as motorized or rotary ball valves) are powered by a motor and gear train. These are the most popular choice for ball valve automation. If no air supply is available to power pneumatic devices, electric actuators are used.
The most common motors are supplied in 120AC, 24DC and 12DC voltages. The motor, when supplied with voltage, engages a gear train which produces the torque necessary to cycle the ball valve.
In the case of Gemini Valve’s electrically actuated ball valves, this torque rotates a shaft that is connected to the stem of the ball valve. An external SPDT (Single Pole Double Throw) switch or device is used with the electrically actuated ball valve to control the position, either open or closed.
With the Gemini Model 600, starting with the ball valve in the closed position and applying power to “terminal 2” on the internal actuator terminal strip, the actuator shaft rotates 90° at which time an internal cam switch shuts off the motor. The ball valve is now in the open position. Using the external SPDT switch, the power is then applied to “terminal 3”, causing the actuator shaft to rotate 90° at which time another internal cam switch shuts off the motor. The ball valve is now in the closed position. This cycling process takes approximately 6 seconds. Gemini’s electric actuator also features a fold out manual override handle to enable the valve to be operated in the event of loss of power.
Pros & Cons of Electric Actuators | |
Pros | Cons |
|
|
The Differences: Electric vs. Pneumatic Actuators
Power Source
The biggest difference between electric and pneumatic actuators is the driving force of their operation.
Pneumatic actuators require an air supply of 60 to 125 PSI. The solenoid (pilot) valve is controlled by either an AC or DC voltage.
When no air supply is available, electric actuators are used.
Component Size
Double-acting pneumatic actuators are up to 70% smaller in size compared to electric actuators.
Speed
To open or close the valve, pneumatic actuators take 1⁄2 a second to 1 full second, depending on the model. Gemini’s electric actuators take approximately 6 seconds, while other manufacturers can take upwards of 25 seconds or more.
Temperature
Pneumatic actuators are suitable for a wide variety of ambient temperatures, and are rated to operate in temperatures between -20°F and 350°F. Electric actuators can be at risk of overheating in high temperature applications and are often rated between 40°F and 150°F. However, the temperature restrictions will vary depending on the product and the company’s guidelines for rating their products.
Durability & Longevity
High quality rack & pinion style pneumatic actuators can cycle on or off up to 1,000,000 +/- times when used within specifications. Electric actuators have cycles of 250,000 +/- but are application dependent.
NEMA Ratings
The National Electrical Manufacturers Association (NEMA) sets guidelines for the use of actuators in specific environments, like hazardous areas or locations affected by water and debris.
Pneumatic actuators are explosion proof, though care must be taken when paired with a flush mounted solenoid valve. Electric actuators are designed to the following most-common NEMA ratings:
- NEMA 4: Water-tight and intended for indoor or outdoor use. This rating sets a level of protection against dirt, water and ice.
- NEMA 4X: Similar to NEMA 4, with an additional level of protection against corrosion.
- NEMA 6: Submersible, with design dependent on the specified conditions and time.
- NEMA 7: Designed for indoor applications and certain hazardous environments. Capable of withstanding pressure from internal explosions.
Spring-Return
A safety feature for valve actuators is a spring-return or failsafe option. In the event of a power or signal failure, the spring-return sets the valve to the “safe” position determined by the operator.
Spring-return failsafe options are widely available for pneumatic actuators. However, this feature is not as easily implemented with electric actuators.
Cost
Pneumatic ball valves generally have a lower purchase price than electric ball valves. When used within specifications, they have a longer lifespan and may deliver the best overall value depending on your application.
Pneumatic Actuators | Electric Actuators | |
Power Source |
|
|
Common Component Sizes |
|
|
Open/Close Speed |
|
|
Temperature Range |
|
|
Lifespan/Cycles |
|
|
Spring-Return Options |
|
|
Industry Examples |
|
|
How to Select the Right Actuator
Pneumatic Actuators
If your facility has access to compressed air, you can explore the following pneumatic actuators:
- Double-Acting Pneumatic Actuated Ball Valves
These are intended for low to high-cycle applications that require a power outage failsafe and compact design.
- Spring-Return Pneumatic Actuated Ball Valves
This option is designed for moderate-cycle applications that require a failsafe in the event of compressed air or power loss.
- Double-Acting Pneumatic Actuated Ball Valves (with Failsafe)
Use these actuators for high-cycle applications that require a failsafe in the event of compressed air or power loss.
Electric Actuators
If your facility or OEM equipment doesn’t have access to pressurized air, pneumatic actuators won’t be an option. Electric actuators are also popular in applications where a slower cycle time is required. The fast ½ second cycle times offered by pneumatic actuators can be a detriment in high flow applications due to water (or other liquid media) hammer caused by the abrupt stop of media when cycling the valve.
Gemini Valve is happy to help you find the perfect ball valves for your project. Just contact us to get started.
Your Complete Guide To Valve Actuators
A comprehensive introduction to valve actuators, covering power sources, failsafes, questions to ask and more.