Ball Valve Actuator Types: Manual, Pneumatic, Electric & Hydraulic
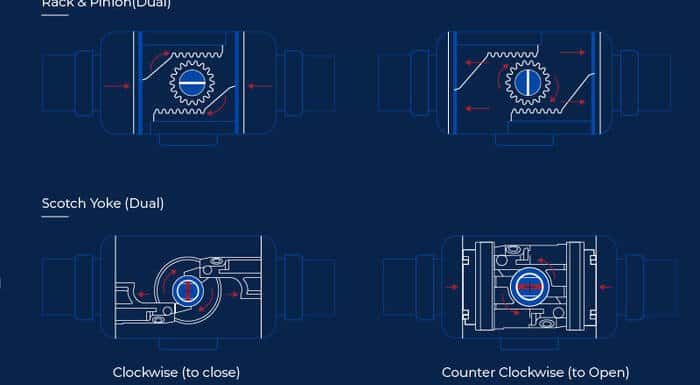
Choosing the right type of valve actuator is crucial for operational efficiency. By using the appropriate power source for your application, you can reduce maintenance expenses, increase uptime and maximize safety.
In this article, we explain the operation of manual, pneumatic, electric and hydraulic actuators, as well as the requirements and considerations to make before selecting a power source.
Read on for the details:
What is a Valve Actuator?
To “actuate” means to put something into motion. For valves, actuators are mounted to the valve stem and work as control mechanisms to open or close the valve.
Valves are either powered manually or by automated energy sources including:
- Electric
- Pneumatic
- Hydraulic
Types of Valve Actuators
Valve actuators are classified by their motion. For example, the two most common types of valve actuators are rotary and linear. Both can be powered by electric, pneumatic or hydraulic energy sources.
Rotary Actuators
Rotary actuators turn in a circular motion and are most often used for the following:
- Ball valves
- Plug valves
- Butterfly valves
Linear Actuators
These actuators move objects on a straight line, such as a back and forth motion, and are used for:
- Globe valves
- Gate valves
- Pinch valves
Rotary valves are available in convenient, compact sizes and offer fast cycle times. Linear valves (globe or gate valves) can be superior to rotary valves (ball valves) when modulation (or throttling) is required. This refers to the actuator’s ability to stop the valve in multiple positions, instead of a simple on/off operation. For applications that require precise control over the flow of media, this enables you to have the valve completely closed, partly open, halfway open or completely open.
Modular actuators are available for ball valves, but these are not always the right solution. This is because as the ball rotates, the amount of flow increases at an exponential rate. It is much more difficult to precisely control the flow through a ball valve than it is with a linear valve such as a globe valve or gate valve.
Manual Valve Actuators
The tried-and-true method of manual operation is also an option to power valves in certain scenarios.
These valves are powered by hand using levers, handles or wheels to move the valve stem. Although these can be easy to work with and inexpensive to operate, they are not designed for large valves or valves in remote locations.
The Different Types of Manual Valve Actuators
Basic Levers | These are considered the standard handle option. |
Latching-Lockable Lever Handle | This option includes a lever handle that prevents the valve from accidentally opening or closing. |
Oval Handles | This compact handle option is intended for applications where the valve may be in close proximity to other devices. The design also minimizes accidentally opening or closing the valve. |
Hand Wheels | Larger valves with high torque requirements typically use hand wheels. These are commonly used as actuators on butterfly valves. If a valve is too high to reach, chain wheels can be added to a gearbox for easy on-the-ground operation. |
Manual Valves with Limit Switches | A limit switch is a position indicator that communicates the valve to the control system. |
Pneumatic Actuators
Pneumatic actuation requires a power source of pressurized air or gas to automate the control of a valve. This type of actuation doesn’t rely on a motor but electricity is necessary if the component is paired with an integral pilot or a solenoid valve.
The Different Types of Pneumatic Valve Actuators
Rotary Actuators | Quarter-turn valves, like ball valves, butterfly valves and plug valves, can utilize two different types of rotary actuators: rack and pinion and scotch yoke. Both work by converting linear motion into rotational motion.
Rack and pinion designs include a piston, rack and pinion. According to Technology.org, “as air pressure increases on one side of the piston, it moves the rack inwards and through a gear connection with the pinion it spins the output rotary shaft.” Rack and pinion actuators are found across the chemical, pharmaceutical, water processing and oil and gas industries. Scotch yoke designs feature a linear-moving piston connected to the rotary shaft by a pin and slot mechanism. “As the air pressure increases and moves the piston linearly, it spins the rotary shaft through a cam system (pin and slot),” Technology.org explains. “This will then in effect turn the valve and either open or close it.” Scotch yoke actuators are typically found in chemical and general process applications. |
Double-Acting Valves | These valves use compressed air to open and close the valve. If there is a loss of power, the ball valve will return to the closed position. Double-acting valves are ideal for low to high-cycle applications. |
Spring-Return Valves | In a spring-return ball valve, air is used to open the ball valve while a failsafe spring forces the valve closed. This ensures that the valve will fail closed in the event of a power loss or compressed air failure. These valves are intended for low to moderate cycle applications.
|
Solenoid Valves | These valves control the flow of air going to the pneumatic actuator. Solenoid valves can be used to pilot the actuator remotely or can be flush mounted directly to the actuator. For applications that utilize multiple pneumatically actuated valves, solenoid banks are often used so that a solenoid valve is not required for each individual actuator.
|
Key Considerations of Pneumatic Valve Actuators
- Power Source: Pneumatic actuators require an air supply of 60 to 125 PSI.
- Speed: To open or close the valve, pneumatic actuators take 1⁄2 a second to 1 full second, depending on the model.
- Duty Cycle: Pneumatic actuators have cycles (on/off) of 1,000,000 +/- when used within specifications.
- Safety Features: Spring-return and failsafe options are widely available for pneumatic actuators.
Electric Actuators
For facilities or applications without access to pressurized air, electric actuators are recommended. Also known as motorized valve actuation, this option uses a motor and voltage to power a valve.
Most electric valves have slower index times compared to pneumatic. For applications with high velocity or pressure, electric actuation can prevent water hammer. Rotary and linear options are available to electric actuators.
Key Considerations of Electric Valve Actuators
- Voltages: Most commonly, motors are supplied in 120AC, 24DC and 12DC voltages. With a voltage supply, the motor engages a gear train to produce the necessary torque to cycle the ball valve.
- Duty Cycle: Electric actuators have cycles of 250,000 +/- but this is application dependent.
- Speed/Torque Options: Most electric actuators take approximately 6 seconds to open/close the valve. The exact time will depend on the gearing and size of the actuator body.
- Protection Ratings: The National Electrical Manufacturers Association (NEMA) sets guidelines for the use of electric products in certain environments. Below are four of the most common ratings for electric actuators:
- NEMA 4: Weatherproof, for indoor and outdoor use. This rating defines the necessary protection needed against water, dirt and ice.
- NEMA 4X: This rating follows the NEMA 4 guidelines with added protection from corrosion.
- NEMA 6: For submersible use in water, quarries and mines. The exact design depends on the specific pressure and time the product is submerged.
- NEMA 7: For indoor use in hazardous areas. This rating means products are capable of withstanding pressure from internal explosions.
Related Reading: Pneumatically vs. Electrically Actuated Ball Valves: Which Should You Use? >>
Hydraulic Actuators
Hydraulic actuators are similar to pneumatic devices, only they use pressurized fluid instead of air or gas. The fluid — either water or oil — is fed to one or both sides of a piston to create movement. Hydraulic actuators can power both linear and rotary valves, and are most commonly used for offshore and upstream applications.
There are two different types of hydraulic actuators:
- Single-Acting: Pressurized fluid actuates the valve in one direction. A compressed spring actuates the valve in the other direction.
- Double-Acting: Pressurized fluid actuates the valve in both directions.
Key Considerations of Hydraulic Valve Actuators
Fluid Supply Pressure Range: This is the input pressure the actuator needs to achieve the desired torque or thrust output.
Gemini Valve is here to help you find the right ball valve actuator for your application. Contact us to get started.
Your Complete Guide To Valve Actuators
A comprehensive introduction to valve actuators, covering power sources, failsafes, questions to ask and more.