Valve Stem Packing
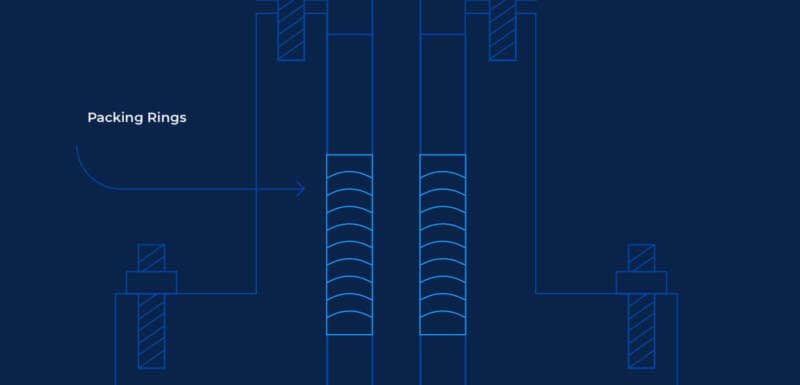
In the vast majority of valve designs, stems are an essential component responsible for opening and closing the valve’s sealing element in response to signals from a control mechanism. Valve stems are typically made of metal and are attached to the valve’s actuator, which moves the stem in response to signals.
The valve stem passes through the valve body and seals against a seat to stop the flow of fluid through the valve. In order to prevent leaks, stem-actuated valves require some form of packing or seal around the stem. This packing serves to create a barrier between the stem and the valve body, preventing fluid from leaking out. Continue reading to learn more about valve stem packing and how it can benefit your piping applications.
What Is Valve Stem Packing?
Valve stem packing refers to the sealing components used to prevent leaks from the stem of a valve. Valve stem packing plays a critical role in ensuring a long service life for the valve.
The packing material is typically made of a soft, pliable material, such as plastics, soft metals or braided fibers. These materials are chosen for their flexibility, durability and ability to create an effective seal. A packing nut or gland is typically used to apply pressure to this packing and create a tight seal. Seals can vary in shape and size depending on the valve.
Valve packing is typically affordable and dependable, and some valves may be designed so that the packing is easy to replace, reducing maintenance costs over time.
Valve Stem Packing Material
There are many materials commonly used for valve stem packing. Some of the most commonly used include the following:
- PTFE (Polytetrafluoroethylene), also commonly known as Teflon®, is one of the most popular valve seal materials, favored for its low friction coefficient and wide temperature range. PTFE is also highly chemically inert, making it compatible with a very wide range of potential media.
- Graphite offers less longevity than PTFE in the vast majority of applications but is often favored in applications with very high temperatures that exceed the threshold of what PTFE or similar plastics can withstand.
- Elastomers are commonly used for their flexibility and resilience. They also tend to be easy to install and are commonly used in valves that are designed to be serviceable. The most common elastomers used in valves are EPDM, Fluoroelastomer, Buna-N, and silicone. Elastomers are sometimes coated in PTFE to improve chemical compatibility.
- Carbon Fiber is often used for its strength and stiffness and can be an effective seal in high pressure applications that other materials may not withstand. This material also has low thermal expansion which allows it to perform well in certain applications with severe temperature variation.
No matter what substance is used to pack a valve stem, the material is compressed to establish a pressure seal between the liquid inside the valve body and the exterior atmosphere. The key factors to consider when selecting a valve packing material are:
- Media Compatibility: The fluid or gas that will be flowing through the valve must be chemically compatible with the seal material.
- Pressure Resistance: The valve seals must be suitable to withstand the pressure that the liquid or gas media will be under.
- Temperature Sensitivity: The temperature of the media will directly impact the sealing properties of the packing material.
Common Challenges of Valve Stem Packing
Although valve stem packing is an essential component, it can also pose a few challenges, specifically when it comes to maintenance and replacement. Valve stem packing is not infallible and will begin to wear and relax (or loosen up) over time, which can make your valve vulnerable to leaks.
The aftermath of a leak can not only be pricey to repair but can also put you and the environment at risk of chemical exposure (depending on the type of media involved in your processes). It is essential that you catch and address a packing leak early to avoid exposure and damage to your piping system.
To replace the valve stem packing, remove the valve from service and remove the actuator from the valve. Next, you will need to separate the valve body in order to access the packing box. Always refer to your product instruction guide or reach out to a Gemini Valve representative to ensure you carry out the disassembly steps correctly.
A few other common challenges associated with valve stem packing include:
- Wear and Tear: The packing is generally the component that is most susceptible to wear and is the first thing to check in the event of a leak.
- Improper Installation: Incorrect installation of the valve stem packing can lead to uneven pressure distribution, inadequate compression or misalignment. This can result in leaks and premature wear.
- Abrasive Media: Particulates in the media flowing through the valve can cause valve seals to wear rapidly. Conversely, media with lubricative properties can greatly extend the lifespan of the valve packing.
- Cavitation: In applications where cavitation occurs, the formation and collapse of vapor bubbles can cause erosion of the packing material.
- Water Hammer: Water hammer can generate significant noise and vibration within the pipeline. These vibrations can affect the packing materials and the overall stability of the valve, potentially leading to issues with the packing’s performance.
Want to learn even more about valve stem packing and whether you need it for your next project? Contact an expert at Gemini Valve today to get started.